ALUCOBOND®
ALUCOBOND®
Known across the world as ‘the original’ ALUCOBOND® has been the market leader in aluminium composite panels since 1969.
ALUCOBOND® is known for its incredible properties, such as extraordinary flatness, a large variety of colours, and perfect formability. It has been developed to be both a rigid and flexible fascia material for architecture and is extremely weatherproof, impact-resistant, and break-proof, vibration-damping, and ensures easy and fast installation.
As a light composite material consisting of two aluminium cover sheets and a plastic core, this incredibly versatile product is also preferred in areas other than architecture – such as corporate design – and is widely used in industry and transportation.
ALUCOBOND® sold over a million sq.m of cladding material worldwide and has been awarded with numerous international prizes.
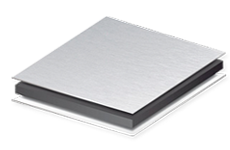
PRODUCT PROPERTIES
ALUCOBOND® is a composite panel consisting of two aluminum cover sheets and a polyethylene (virgin LDPE) core. The superb properties of this material offer architecture an inspiring new range of solutions – whether your project is a private home or a public building, corporate headquarters, office, or a trading/industrial complex – everything is possible with ALUCOBOND®.
It is also used extensively by organizations planning to create a new corporate design for retail chains, car showrooms, banks, petrol stations, etc.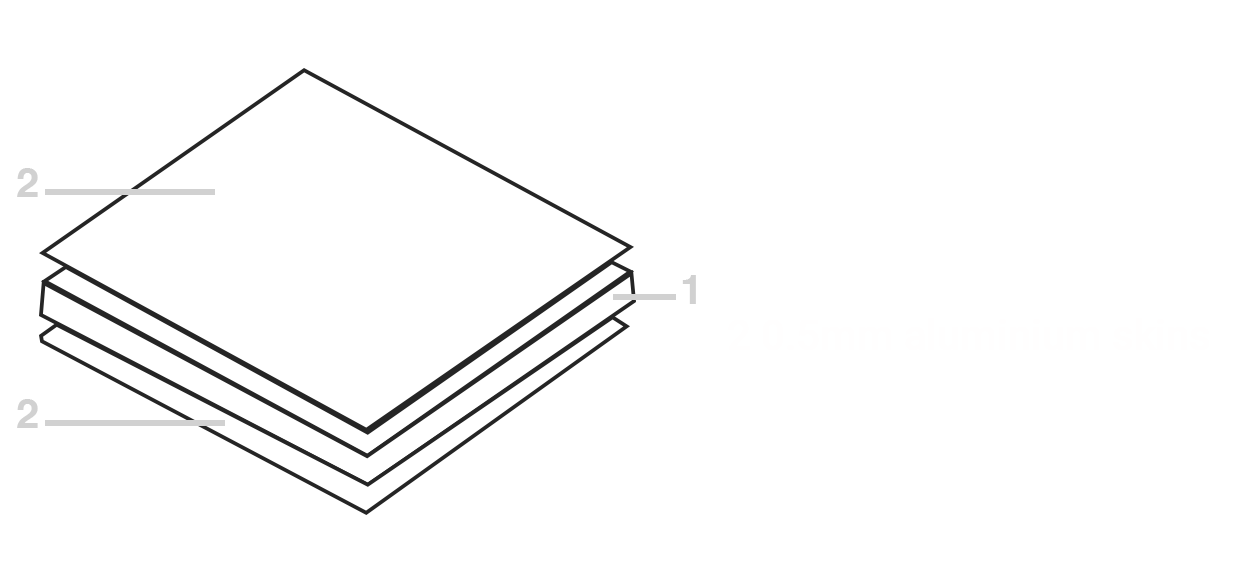
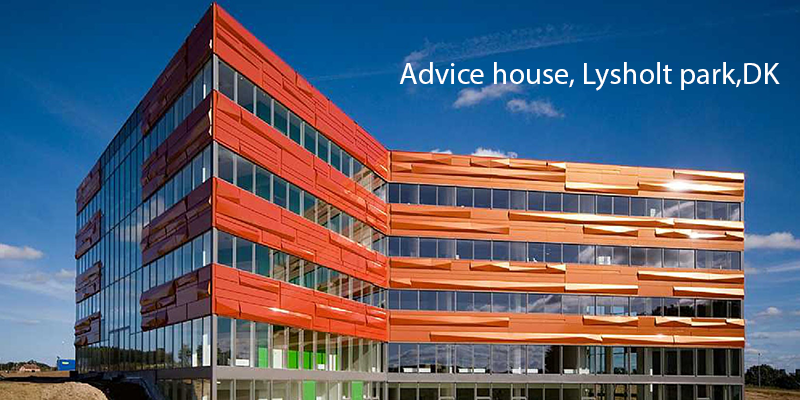
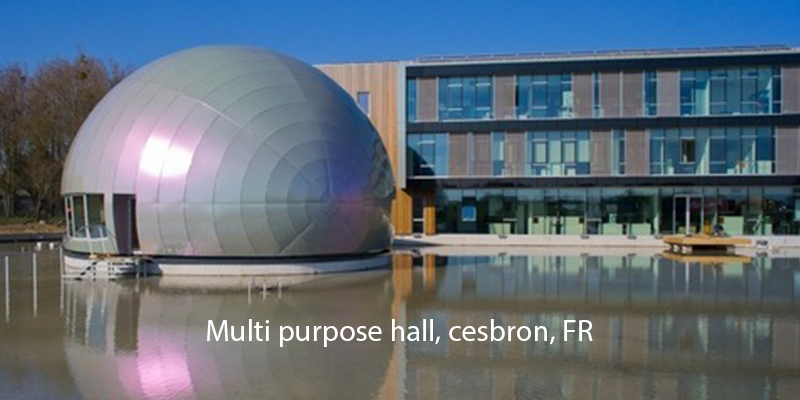
Lightness meets rigidity
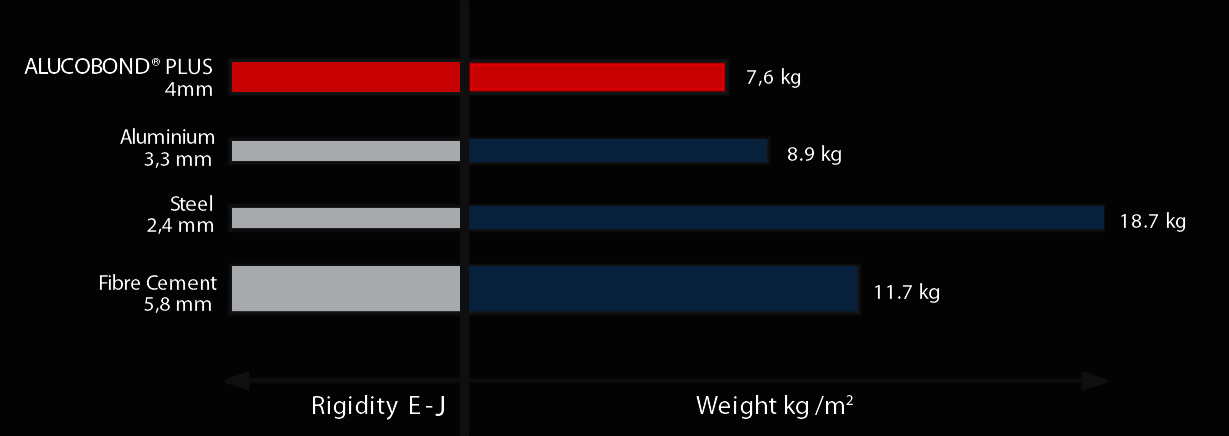
Sustainability
3A Composites is the parent company of ALUCOBOND® and is recognized across the globe as one of the leaders in the field of sustainability. Its reputation is spread far and wide, including among other diversified producers and raw material processing companies around the world.
The company’s unflinching commitment to sustainability – along with taking the needs of all key groups into account – enables it to make decisions of the highest economic, social, and ecological value. 3A Composites also commits to continuous self-improvement programs for environmental protection, many of which exceed government regulations.ALUCOBOND® Lifecycle
Over decades of use in a rear-ventilated cladding system, ALUCOBOND® protects a building from weathering and the harmful effects of industrial and environmental pollution. It also acts as a barrier against solar radiation; the ventilated space between the ALUCOBOND® panels and the wall or the thermal insulation reduces heat transmission.
ALUCOBOND® also protects the wall of a building from high and rapid temperature changes; moisture can pass through the wall, yet the building structure remains dry.
During the lifecycle of ALUCOBOND® composite panels, no substances containing CFC are set free at any time. The core material does not contain any nitrogen, chlorine, or sulfur – therefore, it is the perfect choice for projects which require environmental-friendly materials.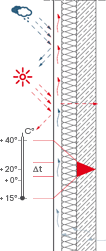
The major advantages
- Lower maintenance costs
- Long-term preservation of the building’s structure
- During winter there are major savings in heating costs
- In summer there are major savings in air-conditioning costs
- Reduction of thermal expansion
- Reduction in crack formation
Recycling
PRODUCT RANGE
ALUCOBOND® Thickness: 3/4mm
Width (mm) | 1000 | 1250 | 1500 | 1575 | 1750 |
---|---|---|---|---|---|
Length (mm) | 2000-6800 | 2000-6800 | 2000-6800 | 2000-6800 | 2000-6800 |
Solid Colours | ![]() |
![]() |
![]() |
![]() |
![]() |
Metallic Colours | ![]() |
![]() |
![]() |
![]() |
![]() |
ALUCOBOND® Spectra & Sparkling | ![]() |
![]() |
![]() |
![]() |
— |
ALUCOBOND® naturAL | — | ![]() |
![]() |
— | — |
ALUCOBOND® Legno – Premium Wood | ![]() |
![]() |
![]() |
— | — |
ALUCOBOND® Anodized Look | ![]() |
![]() |
![]() |
![]() |
— |
ALUCOBOND® Design | ![]() |
![]() |
![]() |
— | — |
ALUCOBOND® Anodized* | — | ![]() |
![]() |
— | — |
Footnotes:
on request
Dimensional Tolerances
TECHNICAL DATA
THICKNESS | CODE | STANDARDS | UNIT | 3MM | 4MM | 6MM |
---|---|---|---|---|---|---|
Thickness of Aluminium Layers | [mm] | 0.5 | ||||
Weight | [kg/m²] | 4.5 | 5.5 | 7.3 | ||
Width | [mm] | 1000 / 1250 / 1500 | ||||
TECHNICAL PROPERTIES | CODE | STANDARDS | UNIT | 3MM | 4MM | 6MM |
Section modulus | W | DIN 53293 | [cm³/m] | 1.25 | 1.75 | 2.75 |
Rigidity | E·J | DIN 53293 | [kNcm²/m] | 1250 | 2400 | 5900 |
Alloy / Temper of Aluminium Layers | EN 573-3 EN 515 | EN AW 5005A (AIMg1) H22/H42 | ||||
Modulus of Elasticity | EN 1999 1-1 | [N/mm²] | 70’000 | |||
CORE | CODE | STANDARDS | UNIT | 3 MM | 4 MM | 6 MM |
Polyethylene, Type LDPE | [g/cm³] | 0.92 | ||||
SURFACE | CODE | STANDARDS | UNIT | 3MM | 4MM | 6MM |
Lacquering | Coil Coating Fluorocarbon based (e.g. PVDF) | |||||
Gloss (initial value) | EN 13523-2 | [%] | 30-80 | |||
Pencil Hardness | EN 13523-4 | HB-F | ||||
ACOUSTICAL PROPERTIES | CODE | STANDARDS | UNIT | 3MM | 4MM | 6MM |
Sound Absorption Factor | αs | ISO 354 | 0.05 | |||
Sound Transmission Loss | Rw | ISO/DIS 717-1, EN ISO 140-3 | [dB] | 25 | 26 | 27 |
Loss Factor | d | EN ISO 6721, Frequency range 100-3200 Hz | 0.0072 | 0.0087 | 0.0138 | |
THERMAL | CODE | STANDARDS | UNIT | 3MM | 4MM | 6MM |
Thermal Resistance | R | DIN 52612 | [m²K/W] | 0.0069 | 0.0103 | 0.0172 |
Heat Transition Coefficient | U | DIN 4108 | [W/m²K] | 5.65 | 5.54 | 5.34 |
Temperature Resistance | [ºC] | -50 to +80 |
Wind load and permissible panel sizes
ALUCOBOND® A2 3 mm
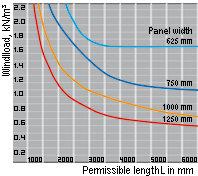
ALUCOBOND® A2 4 mm
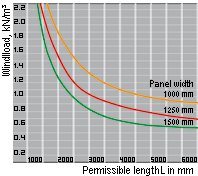
FIXING SYSTEMS
FIRE CLASSIFICATION
Country | Approval | Name | Approval Authority |
---|---|---|---|
Belgium | UBATc 99/2368 | ALUCOBOND® Cassettes; Bardage rapporté | UBATc, Bruxelles |
Czech Republic | c.216/C5a/2009/0148 | ALUCOBOND® | PAVUS a.s., Praha |
France | n° 2/09-1372 | ALUCOBOND® Riveté | CSTB, Paris |
France | n° 2/09-1371 | ALUCOBOND® Cassettes | CSTB, Paris |
Country | Approval | Name |
---|---|---|
EU | EN 13501-1 | Class D |
Germany | DIN 4102-1 DIN 4102-7 |
Class B2 passed |
France | NF P 92-501 NF F 16-101 |
Class M1 Class F0 |
INSTALLATION | MAINTENANCE | STORAGE | HANDLING GUIDELINE
Dimensional tolerances | ||
---|---|---|
Thickness | ±0.2 mm | |
Width | -0 / +4 mm | |
Lengths | 1000 – 4000 mm | -0 / +6 mm |
Lengths | 4001 – 8000 mm | -0 / +10 mm |
Protective foil
- To avoid residuals of glue sticking to the surface of the panels due to UV radiation, it is recommended to remove the protective foil as soon as possible after the installation.
- The protective foils and the panel surfaces must not be marked using ink (marker), adhesive tapes or stickers, as the lacquered surfaces could be damaged by solvents or plasticizers.
- Make sure to remove the protective foil as soon as possible after installation as weathering for a longer period could make the foil difficult to remove.
- Cleaning and maintenance
Cleaning and maintenance

ALUCOBOND®
Download our Alucobond processing manual
Storage / Handling
- Protect ALUCOBOND® pallets during storage against rain, penetration of moisture and condensation.
- Only pallets of identical size should be stacked, with a maximum of 6 pallets stacked on top of each other.
- Storage exceeding 6 months should be avoided, as it may become difficult to remove the protective foil.
- When stacking the panels nothing should be placed in between them, as this could produce marks on the panels.
Recycling
PROCESSING
Blade geometry | Tooth thickness approx. 2 - 4 mm, tapered to the inside to prevent jamming |
Tooth geometry | Trapezoid tooth / flat tooth |
Pitch t | 10 - 12 mm |
Clearance angle α | 15° |
Rake angle γ | 10° positive |
Maximum cutting speed v | 5000 m/min |
Maximum feed s | 30 m/min |
Saw blade-Ø | D = 300 mm (for Striebig vertical panel saw Standard II) |
Number of teeth | t = 72 (for cuts of up to 5 panels) LEUCO Code No. 181724 t = 96 (for single cuts without burrs) LEUCO Code No. 181725 |
Saw blade-Ø | D = 250 mm (for Holz-Her vertical panel saw 1255 ALUCOBOND®) |
Number of teeth | t = 60 (for cuts of up to 5 panels) LEUCO Code No. 181726 t = 80 (for single cuts without burrs) LEUCO Code No. 181727 |
Bore ø | D = 30 mm |
Tooth thickness | 3.2 mm |
Clearance angle α | 15° |
Rake angle γ | 10 ° positive |
- For clean cuts use sharp tools and dies with minimal cutting clearance (0.1mm). Punching will cause a slight deflection at the cut edge of the impact side.
- Holes having a minimum diameter of 4mm can be punched.
- Distance between the adjacent hole edges should not be less than 4mm.
- Please ask for detailed information on how to perforate ALUCOBOND® before proceeding.
- While using a jigsaw, use saw blades that are used for cutting wood and plastic material.
- Cut abrasively while using a waterjet cutting machine. Predrilling of panels is required before commencing.
- While using a waterjet, a cut is needed in the middle of the panel as it is not possible to drill through using a waterjet.
- CNC machining centres should use a one edge cutter.
- The minimum required radius is r = 10 x t (t = panel thickness).
- The spring-back effect of ALUCOBOND® is greater than that of a solid aluminium sheet.
- The die edges should be rounded and smooth.
- To prevent damage to the panel surface, protective foil must not be removed during bending.
- Additionally, the visible surface can be protected by using plastic pads of 1-2mm thickness
- Ideal die width: 2 x t + 2 x protective foil thickness + punch diameter + 15mm
- Before scaled-up production, testing on the sample panels is recommended.
A = punch
B = protective foil
C = die
D = die width
r = radius
- ALUCOBOND® can be bent using a roll bending machine (3 or 4 rollers). Make sure that the feeder does not exert too much pressure. Bending rollers which are also used for bending other metals must be thoroughly cleaned from swarf before processing ALUCOBOND®. Make sure to use only polished rollers free of dents and other defects.
- To prevent damage caused to the panel surface, the protective peel-off foil must not be removed during bending. Additionally, the visible surface can be protected by using plastic pads of 1–2mm thickness.
- Before scaled-up production, testing on the sample panels is recommended.

- Low investment cost
- Simple fabrication technique
- Folding can be done on site, saving transportation cost
- Low-cost fabrication of shaped components used in fascia and wall cladding, roof edgings, column cladding, flashings, etc.
- Flexibility in creating shapes
- Very economical
- Shapes are not limited by machine capacity
- The fabrication of shaped components using ALUCOBOND® only requires a minimal investment outlay.
- Hand routers and sheet milling machines are inexpensive and can be used either in the workshop or on site.
- The fabrication of shapes in larger quantities is particularly economical using vertical panel saws equipped with ALUCOBOND® grooving accessories.
For outdoor use please note:
- Use aluminium blind rivets that have been approved for construction with a 5mm shaft diameter and an attachment head diameter of 11mm or 14mm.
- Please take the thermal expansion of the panel into account (2.4 mm/m/100°C). To avoid jamming, the hole in the panel must be large enough to allow for expansion.
- With the shaft of the rivet fitting closely to the edge of the hole, the attachment head must cover 1mm of the area surrounding the hole.
- Multi-step drills or sleeves with corresponding diameters are used for centrically drilling holes into the panel and the substructure for centrically fitting the rivet.
- Rivet attachment jigs are used for fitting blind rivets without jamming, allowing for a tolerance of 0.3mm.
- Make sure to use rivet attachment jigs and rivets from the same manufacturer, as the height of the attachment head according to DIN 7337 may vary.
- The clamping thickness results from the thickness of the material to be riveted plus an additional value of 2mm to ensure that the closing head is perfectly formed. In accordance with this clamping thickness the corresponding shaft length is determined in the tables provided by the rivet manufacturers. (Lmin = 14 mm).

Threaded fasteners for outdoor use
Threaded fasteners for indoor use
Threaded fasteners for outdoor use
For outdoor use make sure to take the thermal expansion of the panel into account. To avoid jamming, the hole diameter in the panel must allow for the expansion. Fastening without jamming is possible using fascia screws made of stainless steel with sealing washer (Fig. 1) that have been approved for construction. The screws must be suitable for the corresponding substructure (please note the information given by the manufacturer). The screws should be tightened with a torque wrench or screwdriver so that the sealing washer is placed on the panel for sealing the bore hole without exerting pressure to the panel. Multi-step drills or sleeves having corresponding diameters are used for centrically drilling holes into the panel and the substructure and for centrically fitting the rivet. Important: Make sure to remove the protective foil in the screwing area prior to screwing.Threaded fasteners for indoor use
Screws for sheet metal and wood with different head-shapes are suitable for indoor use (Fig. 2). They do not normally allow for any panel expansion. Countersunk screws can be inserted by the usual countersinking method or by depressing the aluminium surface into the panel. When depressing the aluminium surface, the hole diameter in the panel must be larger than the screw diameter.